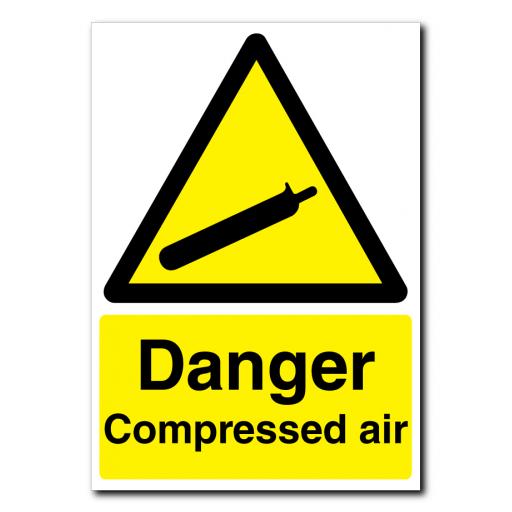
The following precautions pertain to the use of compressed air in machine shops:
1. All pipes, hoses, and fittings must have a rating of the maximum pressure of the compressor. Compressed air pipelines should be identified (psi) as to maximum working pressure.
2. Air supply shutoff valves should be located (as near as possible) at the point-of-operation.
3. Air hoses should be kept free of grease and oil to reduce the possibility of deterioration.
4. Hoses should not be strung across floors or aisles where they are liable to cause personnel to trip and fall. When possible, air supply hoses should be suspended overhead, or otherwise located to afford efficient access and protection against damage.
5. Hose ends must be secured to prevent whipping if an accidental cut or break occurs.
6. Pneumatic impact tools, such as riveting guns, should never be pointed at a person.
7. Before a pneumatic tool is disconnected (unless it has quick disconnect plugs), the air supply must be turned off at the control valve and the tool bled.
8. Compressed air must not be used under any circumstances to clean dirt and dust from clothing or off a person’s skin. Shop air used for cleaning should be regulated to 15 psi unless equipped with diffuser nozzles to provide lessor pressure.
9. Goggles face shields or other eye protection must be worn by personnel using compressed air for cleaning equipment.
10. Static electricity can be generated through the use of pneumatic tools. This type of equipment must be grounded or bonded if it is used where fuel, flammable vapors or explosive atmospheres are present.