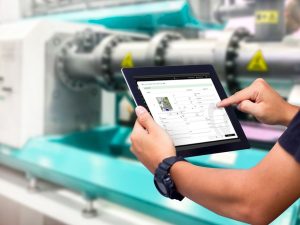
Compressed air is a widely used technology in various industrial and commercial applications. It is an efficient and effective way to power pneumatic tools and equipment. However, compressed air is a costly commodity, and saving compressed air can help businesses reduce their energy costs and increase their productivity. In this article, we will provide you with some tips on how to save compressed air.
Conduct An Air Audit
The first step to saving compressed air is to conduct an air audit. It will help you identify where and how much compressed air is being used, wasted, or lost due to leaks. Air auditing involves measuring the air pressure, flow rate, and usage of air-powered equipment and identifying areas where compressed air is being wasted. The following steps can be taken:
a. Identify the near-empty or constant-use machines
b. Monitor the pressure drop from plant to machine or from a compressor to machine
c. Check pressure levels through gauges and set it as per desired set-points only
Fix Air Leaks
Air leaks are one of the primary causes of compressed air wastage. Even small air leaks can lead to significant costs over time. Therefore, it is essential to identify and fix air leaks as soon as possible. Leaks can occur in many places, such as couplings, hoses, valves, and fittings. The following steps can be taken:
a. Conduct regular leak detection surveys
b. Keep the maintenance logs of machines updated
c. Use sealant or thread locker to fix small leaks
Control the Pressure
Excessive pressures can lead to compressed air wastage and increase energy costs. Therefore, it is essential to control the pressure level based on the equipment’s specifications and requirements. The following steps can be taken:
a. Use regulators to control the air pressure
b. Adjust the pressure according to the requirement of machines instead of keeping it constant
c. Ensure that regulators are installed close to the designated equipment
Use Efficient Equipment
Using efficient equipment can help save compressed air and reduce energy costs. Selecting the right type of equipment for the job can help optimize compressed air usage. For example, using a smaller nozzle can reduce air consumption while still providing sufficient airflow. The following steps can be taken:
a. Choose the right type of equipment based on the application
b. Use a small and efficient nozzle
c. Use larger diameter pipes for extended distances, so the pressure drop is minimized
Turn Off Equipment When Not In Use
Turning off equipment when not in use can help reduce compressed air usage. Many times, equipment can be left running even when not in use, leading to compressed air wastage. The following steps can be taken:
a. The automatic switch-off can be used in machines
b. Workers should be trained and encouraged to turn off equipment when not in use
c. Programmable logic controllers can be used to turn off equipment automatically
Conclusion
Saving compressed air is a crucial aspect of reducing energy costs and increasing productivity. Conducting an air audit, fixing air leaks, controlling the pressure, using efficient equipment, and turning off equipment when not in use are some of the ways to save compressed air. Small changes can lead to significant savings over time, so it is essential to be mindful of compressed air usage and take steps to conserve it.